Industrial Laser Marking Systems / Laser Markers
Laser Marking in the Automotive Industry
-
Tags:
- Laser Marking , Metal , Plastic
The automotive industry has been leading the charge for making laser marking a standard when it comes to part marking and traceability. If a defect is found in an automobile, the manufacturer needs to identify all defective parts and track down when and where those parts were produced. Laser markinng plays an essential role in ensuring this traceability by creating clear and permanent marks containing all the relevant information.
Direct Part Marking in the Automotive Industry
Laser marking automotive parts is a versatile and permanent process that helps identify and track components during and even after the manufacturing process. It’s used to mark text, logos, or other images with a high degree of accuracy and detail. These marks prevent counterfeit parts from entering the market and identify defects on a massive scale.
Laser marking automotive parts is also more durable than other methods, such as labels or ink, and can withstand the high temperatures and harsh environments often found in the industry. Automotive laser marking does not require any consumables to add a direct part mark.
In addition, laser markings can be applied quickly and easily in seconds, making them a cost-effective solution for mass production.
Shift lever
Seat rail
Gear
Bearing
Inverter case
Motor housing
Transmission case
Engine block
This process is essential to identify the make and model of the vehicle, as well as the country of origin. Laser marking is also used to put serial numbers on car parts so that they can be tracked if lost or stolen.
Some of the automotive industry's greatest challenges are safety, part alignment, and product changeover. Additionally, it can be difficult to achieve a consistent and even laser mark on curved or three-dimensional surfaces. Automotive manufacturers must carefully consider these challenges before deciding whether laser marking is the best solution for their needs.
With years of experience working with automotive industry clients, we have developed innovative and reliable products to safely meet these challenges and help you improve and automate your processes.
Learn how KEYENCE laser markers overcome common limitations to make automotive marking quick and easy.
We’re here to provide you with more details.
Reach out today!
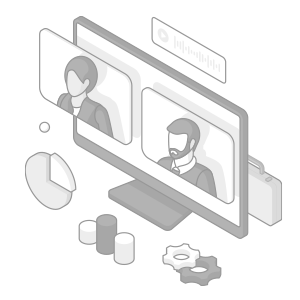
Automotive Parts: Reliability in the Industry
Safety is the #1 concern for manufacturers in the automotive industry. As such, high levels of history management and process control are necessary to ensure proper part traceability. Many automotive manufacturers and part suppliers have found that 2D code marking is a great way to establish this traceability. Part marking was once only required for major components, but it is now steadily spreading to include individual parts used in the construction of automobiles (typically over 20,000!). Considering the rapid increase in part marking, laser markers have become a go-to for manufacturers thanks to their tamper-proof marking and low running costs.
Curious about our pricing?
Click here to find out more.
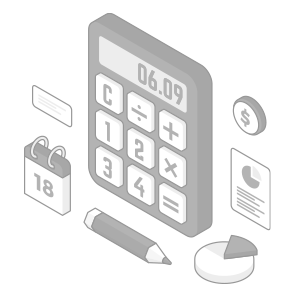
How Direct Laser Part Marking Improves Automotive Safety
The automotive industry produced 1.8 million vehicles on US soil in 2022 and 85 million around the world—imagine how many individual parts that is! Thousands of manufacturing facilities are responsible for each part, meaning that even cars with the same make and model have parts from different facilities.
This ongoing flow of manufacturing is efficient for getting new vehicles on the market every year, but tracing every single part is not simple. The sheer volume of moving parts throughout the manufacturing process is impossible to manage by only identifying the make and model of a vehicle.
Laser marking automotive parts improves the safety of vehicles because it strengthens traceability with precise and permanent marks. The effectiveness of a laser marker translates to identifying vehicle recalls at rapid and organised rates.
Permanency
Laser marking has become a preferred choice in the automotive industry, mainly for its permanency. For one, serial numbers, barcodes, and other part identification marks need to withstand some harsh conditions. This includes exposure to extreme temperatures, chemicals, and abrasion. Unlike other methods, laser marking ensures that these types of marks remain intact and legible over the vehicle’s lifespan.
In addition, the permanency of laser marking is crucial for traceability and quality control in automotive manufacturing. These markings allow for accurate tracking of components through the production process and lifespan of the vehicle. This helps with quality assurance, recalls, and even compliance with industry regulations.
Alternative methods for laser marking automotive parts are ink, sticker labels, and chemical etching. However, these do not provide the permanency that is required for automotive uses and also require consumables.
Precision
As part of automotive manufacturing and assembly, having a precise marking method is important. Laser marking provides this precision and accuracy, allowing for intricate and fine details to be added to small auto components and delicate surfaces. Its tight tolerances also ensure that markings are placed exactly where they are intended without damaging surrounding materials.
2D Code Quality Control
The largest obstacle to managing and tracing parts with 2D codes is ensuring that the codes are readable. KEYENCE laser markers allow operators to perform a two-way quality check for every mark. A built-in thermopile power monitor allows users to measure (with actual values) the power output of the laser while marking is performed. A built-in 2D code reader makes it possible to visualise the ability/inability of reading and overall reading reliability. These two check mechanisms make it possible to ensure high-quality 2D codes.
- Stable marking quality
- Improved yield
- Preventative maintenance
- Stable equipment operation
Auto-focus Feature
Large parts (like engine blocks) are difficult to align with the focal distance of a laser marker while being transported. This often results in focal misalignment, which in turn causes improper marking. 3-Axis laser markers allow you to perform auto-focused marking that can automatically adjust for changes in the focal distance. This eliminates the need for complicated transportation mechanisms and achieves high-quality marking that's always in focus. This feature is most effective in cases where stable quality is demanded, such as 2D code marking.
- Stable marking quality
- Simplifies equipment
- Increased processing speed
- Energy-efficient operation
Simplified Product Change-Over
There are an increasing number of cases in which multiple product types are manufactured with a single die-cast machine. In the past, these machines have had to be retooled to accommodate laser markers (due to their fixed focal distances). With a 3-Axis control laser marker, it is possible to design a flexible setup that supports multiple product types with a single box. Registering the size of the target and area that will be marked makes it possible to switch between product types by just changing the setting number.
- Reduced man-hours for operation
- Simplifies equipment
- Increased processing speed
- Stable marking quality
As you see, automotive laser marking has become an essential tool for automakers, and it shows no signs of slowing down. With more parts on both traditional and electric vehicles requiring marking, having reliable systems and procedures will allow for safe, timely, and efficient operations.
In addition to laser marking automotive parts, we offer a myriad of solutions for industry challenges. We have helped provide:
- Coolant flow control for metalworking machines
- Stamping-based product difference checking
- Crankshaft difference inspection
- Motor core lamination thickness measurement
- Scratch inspections of gears, bushing, and similar objects
- Post-encapsulation inspection for welding bead defects
- Body sealer dispense inspection
- Robot picking of metal parts and batteries
- Connecting rod measurement
- Battery lamination layer alignment
- Appearance inspection of battery housing
- U-pin dimension inspection
- Character recognition for inscriptions on casted parts
- Retaining ring detection
- ECU PCB solder inspection
- Connector terminal bend inspection
- Lithium-ion battery sealing plate top surface welding inspection
- Measurement of large castings and additionally processed components
Discover more about this product.
Click here to book your demo.
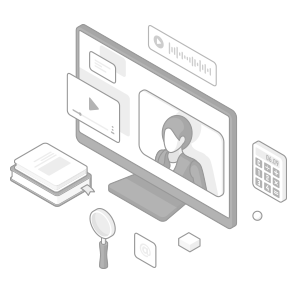
Application Video
FAQs about Laser Marking in the Automotive Industry
Which type of laser is used in the auto manufacturing industry?
Lasers of the infrared wavelength are the industry standard for component marking and processing. Commonly known as fibre lasers, these systems excel at working with metals and present high throughput capabilities appealing to auto manufacturing operations. There is a distinction to be made between marking, welding, and cutting lasers, all of which have their place in the automotive realm. Contact your local specialist to understand how the KEYENCE solution may work for you.
How are lasers used in the automotive industry?
Lasers are used for marking (Traceability, Compliance, Branding), Cutting, and Welding. From raw material to the final assembled components, lasers have the opportunity to facilitate the production process of your components.
What types of laser marking are used in the automotive industry?
The types of automotive laser marking used for vehicle parts are engraving, etching, and annealing.
What is laser engraving?
Laser engraving is a laser part marking process that vaporises a target design and leaves behind an indented mark.
What is laser etching?
Laser etching is a laser part marking process that is best suited for high speed applications. The laser beam alters the target surface reflectivity to produce a contrasted mark.
What is laser annealing?
Laser annealing is a laser part marking process that rearranges a target’s atoms and leaves behind a dark mark without a texture.
Which automotive parts are laser marked?
Parts critical to the end performance of a vehicle are often laser marked to ensure the durability of the tracking and traceability information. Engine, airbag, and axial component manufacturers tend to seek the superior marking permanence provided by laser marking. Brake companies will utilise the flexibility of marking presented by lasers to build brand awareness through marking logos.
Can automotive plastics be laser marked?
Automotive plastics are being laser marked with increased frequency. Developments in the realm of laser marking, such as UV laser systems, have opened the door to working with automotive plastics without the need for material additives. For insight on how KEYENCE's laser marking solutions could work for you, please contact your local representative to learn more.
Why do I need a UV laser for plastic?
A fibre laser’s power may be too strong and distort your part. This is because plastic generally has a weaker heat resistance than metals.
Instead, a UV laser uses a marking method called “cold marking”, which does not have any heat transfer. The cold marking method is gentler on heat-sensitive materials like plastic.