Industrial Laser Marking Systems / Laser Markers
Laser Labelling
Laser labelling is the process of using a laser marking machine to put a label on a product. The label can be used for traceability, identification, or adding regulatory information. Replacing a labeller with a laser can have benefits across many aspects of production.
Using a laser marking machine rather than a standard inkjet printer for labelling will improve value with time, money, and production. Laser markers decrease production time, increase permanency of labels, and decrease use of extra materials.
In addition, manufacturers using laser markers don’t have to deal with consumables such as physical labels, adhesives, or industrial ink. Laser labelling machines are a versatile innovation in the labelling world that can help reduce waste pollution, various costs, and a long list of other benefits, ranging from the manufacturers to the end consumer and even the environment.
Below, we will discuss the differences between laser marking and standard labelling, the characteristics of each, and the best machines to use.
Laser Labelling Machine
KEYENCE offers a UV laser marking machine that marks high-contrast, damage-free, clear labels. To ensure ease of use, this UV laser marking machine contains easy-to-use software that controls the marking. The software can be programmed based on font, size, contrast, materials, and more, depending on your specific requirements.
Comparison of Laser Labelling with Traditional Labelling Methods
When you stack up laser labelling against the capabilities of traditional methods, the differences are glaring. This isn't to say traditional methods are obsolete, but laser labelling is optimal for manufacturing from many standpoints. Some of the main comparisons between the two labelling methods can be found below.
Focal Point | Laser Labelling | Traditional Labelling |
---|---|---|
Permanency
|
Laser Labelling
Laser labelling guarantees permanency throughout the product's lifecycle. It is also more resistant to external stressors such as light and temperature.
|
Traditional Labelling
Known to eventually start to peel and fade with time. Due to the fading print, it can be hard to read vital information.
|
Efficiency
|
Laser Labelling
Laser label machines require very little, to no, maintenance and have no consumables to track or refill.
|
Traditional Labelling
Required to handle consumables, causing downtime in the production process. Switching rolls and ink cartridges are common to this process.
|
Cost-Effectiveness
|
Laser Labelling
With no need to purchase physical labels, laser labelling is very cost-effective and reduces consumable waste and downtime.
|
Traditional Labelling
More expensive due to ongoing consumable purchases. Excess labels can also waste time and money.
|
Visual Quality
|
Laser Labelling
Much more pristine and clear in readable quality. Fewer chances for mistakes or errors in the print.
|
Traditional Labelling
High-quality traditional labelling is possible but susceptible to smudging or rubbing off.
|
Material Compatibility
|
Traditional Labelling
Label adhesives are limited to some degree. They don’t work on every material, even with varying types of adhesive. They’re also bound to lose adhesive strength against the material over time.
|
This table could lay out many other unique differences, but these points provide a comprehensive look at the comparisons. Traditional labelling has been relevant for decades and will be for many more years. Eventually, the evolving nature of labelling and laser marking technology will put conventional methods on the back burner for many people in the manufacturing business.
We’re here to provide you with more details.
Reach out today!
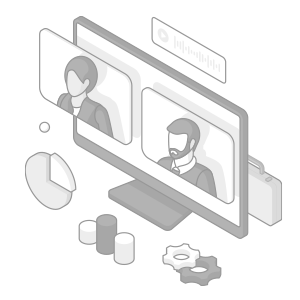
Advantages of Laser Labelling Machines
While comparisons are important, it can be more helpful to review the advantages of direct laser engraving and marking over traditional means. These upsides are pretty universal, regardless of the application.
Some of the most prominent advantages of laser labelling technology include:
- Readability
- Adaptability to varying surfaces
- Reduced downtime and maintenance
- Better cost-effectiveness
- Unmatched permanency
- Better production integrations
- Lesser environmental impact
The list of laser marking advantages goes far beyond this, so it is evident that laser marking will continue revolutionising labelling on many scales. Manufacturers have many angles to consider regarding production, with product authentication and traceability being high on the list.
Curious about our pricing?
Click here to find out more.
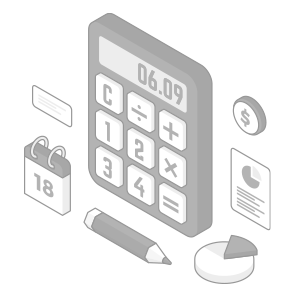
The Role of Labelling and Laser Marking in Product Authentication and Traceability
Laser marking machines also improve product authentication and traceability. Laser labelling systems guarantee uniformity and quality from origin to product integrity and other important details.
Providing a digital footprint for each product that doesn't waver over time will always benefit consumers as well as the manufacturer. These details are equally crucial regarding some aspects of laser labelling requirements within the industry on a local, national, and international level.
We’re here to provide you with more details.
Reach out today!
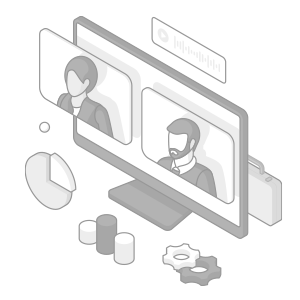
Labelling and Laser Marking Characteristics
Laser markers operate differently than standard labelling systems. Ink labelling systems need extra materials to minimise damage to the product and get an intense mark. These extra materials are usually ink ribbons or thermal heads. Because of the precision of a laser, labelling with a laser marker only requires a UV laser machine.
UV lasers work by passing a standard wavelength through two crystals, which creates a thin laser with high absorption. The high absorption is not synonymous with high heat, a UV laser is gentle on materials and can independently mark without needing protective materials. Because of the high absorption rate, the marks are permanent and do not fade over time.
Inkjet labelling machines were standard, but new laser marking technology outperforms these machines.
Discover more about this product.
Click here to book your demo.
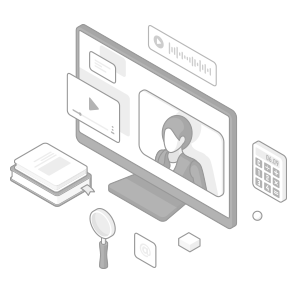