Industrial Laser Marking Systems / Laser Markers
What Is Laser Texturing & How Is It Used?
-
Tags:
- Laser Ablation , Laser Etching , Medical
Surface areas of plastic, metal, or ceramic are naturally smooth, but have you ever touched one of these materials and felt a texture? This doesn’t happen naturally and is made by no mistake. Texturing –adding a natural wood grain, leather, or matte pattern to a material– is added to materials in almost every industry.
From electronics to fashion, using texture for aesthetics, extending lifetime, or producing a high-grade feel, is a widely used manufacturing process. Using a laser marking machine for laser texturing is a quick, clean, and precise way to achieve your texturing goals.
Laser Texturing: What It Is and How It Works
Laser texturing is using a laser beam for texturing a surface area for an improved lifetime, aesthetic, or friction and is becoming more and more popular as a means of increasing adhesive or conductive properties with the rise of the electric vehicle industry. It is used on different materials with ranges of heat resistance and other qualities, meaning that when laser surface texturing, the first step is understanding your material’s characteristics. You may choose metal, plastic, ceramic, or mix. After choosing the material, pick the appropriate laser texturing machine for the material’s heat or corrosion resistance and how intense you want the texturing to be.
Discover more about this product.
Click here to book your demo.
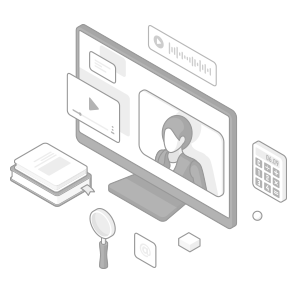
How Does It Differ from Other Surface Texturing Techniques?
Laser texturing uses a light beam emitted by an oscillator, scanned by a mirror, and then focused onto a target. Once the beam hits the target, a process called laser ablation occurs. Laser ablation is quick and automated, with diverse texturing power across a range of materials.
Although laser ablation is a popular method, there are other surface texturing techniques that manufacturers use for the same result. The most common surface texturing technique is called satin-finishing, which is also known as an etching process.
Satin finishing works by first creating a cavity or core mould with a textured pattern on it. The mould is then transferred onto the target product surface, in which chemical etching takes place. The chemical etching then partially removes some materials and leaves behind a textured surface. After that’s done, sandblasting cleans up any imperfections. This process obviously requires many more steps than a laser texturing process and is far less flexible.
We’re here to provide you with more details.
Reach out today!
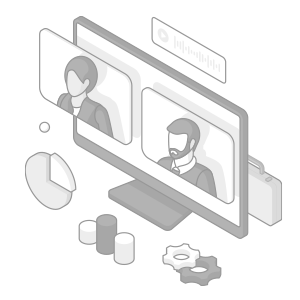
The Science Behind Laser Texturing: How Lasers Modify Surface Structures
As mentioned above, laser texturing uses ablation to create a surface texture. Laser ablation is the process of applying repetitive short yet powerful pulses to a specified target on a whole surface area. Once the repetitive short pulses make the energy of the surface higher than the binding area, the targeted area is removed and leaves behind a textured surface overall. The variation of strength with laser power, speed, and pulse duration affects how the material will be altered.
KEYENCE's MD-X Series Hybrid laser markers excel in these types of applications as they offer a far higher peak power than conventional fibre lasers and better beam control, each decreasing heat effected zone and ensuring there is no change to material properties outside of what is desired.
Laser Texturing Parameters: Exploring the Role of Peak Power and Pulse Duration
- Peak Power
-
"Average power" is commonly referred to as the laser's power. Though the "peak power" is actually much more important when it comes to reaction with the surface of materials for texturing. Generally, higher peak power lasers produce stronger energies instantaneously which reduces heat damage and burning. Even lower "average power" lasers are often able to achieve a higher quality texture quicker than higher power lasers if they are able to achieve this high peak power through oscillation within the laser head.
- Pulse Duration
-
Pulse duration is the length of time that the laser beam directly hits the material. Like speed and power, the duration affects the way the material is texturised and the result. Hybrid laser marking systems such as the KEYENCE MD-X Series are most suitable for texturing/processing applications since they feature a short pulse width and a high peak power. This means there is no need for excessive heat generation which could cause harm to the material. Hybrid lasers are able to achieve a much more uniform finish than conventional YAG or Fibre lasers.
1064 nm wavelength: YVO4 laser / 1090 nm wavelength: Fibre laser
Light wavelength distribution map
Infrared (IR) lasers use the most versatile wavelength of light for marking and processing. IR light is invisible to the human eye because its wavelength is longer than 780 nm (the far end of the visible spectrum).
Lasers that share the same wavelength will have different beam characteristics depending on the oscillation method. In general, high peak power and short pulse durations have stronger instantaneous energy, which reduces thermal damage and prevents scorching.
- General advantages
-
Mark and process a wide range of materials, including metals and plastics.
Get detailed information on our products by downloading our catalogue.
View Catalogue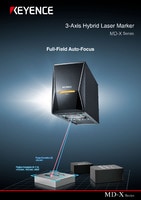
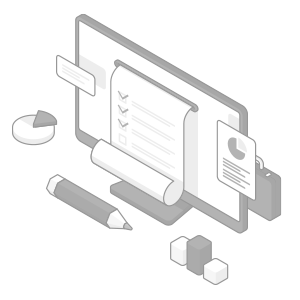
Laser Texturing Techniques: Methods and Approaches
Ablative Laser Texturing: Understanding the Mechanisms and Applications
Ablative laser surface texturing produces different texturing results depending on absorption rate, surface area characteristics, defects, microstructure, and laser texturing machine. For example, using a hybrid laser to texture an onboard instrument panel will use a high peak power and short pulse for limited heat effects.
The Future of Laser Texturing: Trends and Advancements
Laser Texturing in Industry 4.0: The Role of Laser Texturing in Smart Manufacturing
After the White House cited smart manufacturing as a national priority in 2022, the National Institute of Standards and Technology (NIST) released its definition of smart manufacturing as:
"To develop and deploy advances in standards, conformance testing, user-awareness, and adoption of 3D model-based product definition standards to improve product quality and reduce costs for manufacturers throughout the product lifecycle."
Laser texturing already has a role in smart manufacturing because of the automation and advanced software. Common surface texturing techniques require 80% automation – which does not fall into NIST’s requirement of smart manufacturing.
At KEYENCE, our software supports remote manufacturing, so you can monitor all your laser systems through software without visiting the production site.
Nanoscale Laser Texturing: Potential Applications in Biomedical and Optical Fields
In the biomedical and optical fields, research into biocompatibility and the use of nanoscale materials is a hot topic. For products like implants and biosensors, nanoscale laser surface texturing may be the new wave. Laser surface texturing is a non-abrasive process, so it can work on biological molecules, cells, and other materials added to host tissues. Additionally, laser texturing is moving to the nanoscale level and textures microscopic products. Manufacturers are choosing laser technology because of its biocompatibility and fast, clean, and error-free methodology.
We’re here to provide you with more details.
Reach out today!
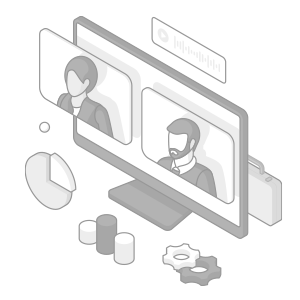