Industrial Laser Marking Systems / Laser Markers
Laser Cleaning vs. Sandblasting Comparison
-
Tags:
- Laser Cleaning , Laser Ablation , Laser Oxide Removal
Rust, dirt, oil, oxidation, resin; these are all problematic top layers that manufacturers commonly need to get rid of. Whether it be for inspection, boosting adhesion, cleaning, or anti-corrosion, removing these layers is a practice used across aerospace, automotive, semiconductor, and heavy machinery industries.
Out of all the ways to get rid of these pesky layers—plasma cleaning, laser cleaning, sandblasting, and chemical etching–laser cleaning and sandblasting cleaning are two methods that reign in popularity. But with different processes, how do you choose which one to use?
In this blog, we’ll discuss the differences between laser cleaning vs. sandblasting so you can make the best choice for your project.
What is Sandblasting Cleaning?
Sandblasting cleaning is a layer removal method for metals. Historically, it’s a method that uses sand, but technicians also use ceramic, glass, and soda grains. Regardless of the medium, sandblasting cleaning works by compressing grains with air and then shooting out of a hose at high speed against a top layer. The top layer is usually rust, oxide, or paint.
Sandblasting removes the layer, and the layer turns into dust and falls to the ground, revealing the substrate underneath.
Sandblasting cleaning is used for getting the contamination off to prevent corrosion, cleaning the top layer off for inspection, or priming it for a new coating or additional manufacturing process. It’s frequently used for the heavy machinery, aerospace, and automotive industry.
We’re here to provide you with more details.
Reach out today!
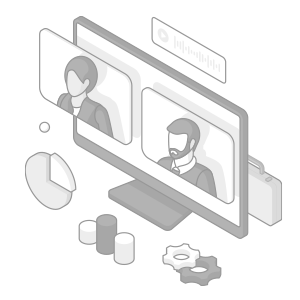
What is Laser Cleaning?
Laser cleaning removes a top layer like oxidation, rust, wire sheath, dirt, oil, enamel, resin, paint, or burrs with laser ablation. Laser ablation is when a laser beam uses short-frequency pulses and high peak power to heat a layer to its evaporation point. Removing the top layer is used for cleaning contaminants or for surface preparation, like anchoring or increasing wettability.
Anchoring is the process of cleaning a part before it is welded or has an adhesive applied. This process controls the bond and improves its adhesion strength. Similarly, wettability is using laser cleaning to improve the control of liquids to avoid pooling or inconsistencies.
A laser cleaning machine is used in industries like automotive, medical, semiconductor, electric vehicle, and battery manufacturing on materials such as resin, metals, rubber, silicon, and ceramic.
Discover more about this product.
Click here to book your demo.
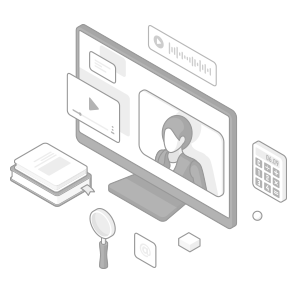
Laser Cleaning vs Sandblasting Differences
Precision
Laser cleaning and sandblasting methods are opposites when it comes to precision.
Sandblasting cleaning uses a hose that sprays out many particles at once. Because of this, sandblasting cleaning is good for large areas because it’s difficult to control the hose precisely.
Laser cleaning is precise because the laser beams are thin and controlled. Since they’re precise, laser cleaning is usually used for smaller or thinner targets or targets that need extreme precision.
Substrate Effect
Since sandblasting cleaning is an aggressive method of removing the top layer, the substrate is often compromised and can be somewhat damaged. In some cases, this isn’t a problem because the substrate damage may not affect the component's functionality.
On the other hand, laser cleaning is a no-contact method of removing a top layer, so there is no effect on the substrate. Since there's no effect, laser cleaning is good for parts that must maintain the substrate for functionality.
Safety
When it comes to the safety of laser cleaning and sandblasting, there is a stark difference. Sandblasting requires a body suit to prevent the media, or the debris generated during sandblasting, from penetrating the skins, eyes, or mouth. In addition to the physical danger that this could pose, there is also risk involved with inhaling this particulate. Lastly, when sandblasting, it is also necessary to be cognisant of your surroundings since the media or debris could damage surrounding components or machinery.
Laser cleaning is a much safer method than sandblasting cleaning, as it only needs goggles. Also, since laser cleaning is so precise, other processing methods/manufacturing processes can be done in the same proximity.
Environmental Impact
Sandblasting cleaning and laser cleaning differ significantly in their environmental impact. Sandblasting uses consumables (the grain) that enter the air. Not only does the grain contaminate the air, but when the grain hits the layer, the layer turns into dust and flakes off as an additional consumable. This process is particularly harmful with layers like lead paint.
Laser cleaning does not use consumables of any kind. The laser beam is a light, and it evaporates the layer with much more control than sandblasting. If laser cleaning happens in a closed environment, there’s no effect on the outside air.
We’re here to provide you with more details.
Reach out today!
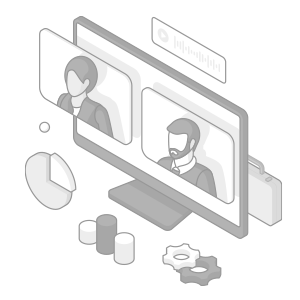
Why Use Sandblasting Cleaning Instead of Laser Cleaning?
Choosing sandblasting instead of laser cleaning is mainly determined by the target application. If the target application is a large metal component that isn’t badly damaged from an affected substrate, then sandblasting may be chosen.
Since sandblasting cleaning shoots out so many particles at once compared to one laser beam, choosing sandblasting for these types of components is a more efficient choice.
Discover more about this product.
Click here to book your demo.
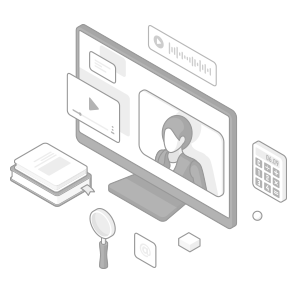
Why Choose Laser Cleaning Instead of Sandblasting?
Choosing laser cleaning instead of sandblasting may be a choice made because of the application, environmental impact, or safety.
If your application is made of material besides metal–such as resin, rubber, or silicon– then laser cleaning is needed. Additionally, laser cleaning is the gentler option if the application cannot have a damaged substrate, such as needing to remove a wire sheath to improve the electrical connection.
Regarding environmental impact and safety, if you’re looking to decrease your environmental impact or lessen cleaning hazards, choosing laser cleaning instead of sandblasting cleaning is the option you need.
We’re here to provide you with more details.
Reach out today!
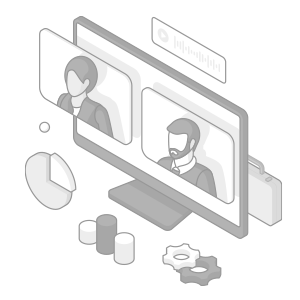
Making the Decision: Laser Cleaning vs Sandblasting
Although laser cleaning and sandblasting cleaning have their differences, they are also both effective metal cleaning methods used by many technicians across industries.
That being said, laser cleaning is a safer, greener, and more versatile way to clean components. At KEYENCE, we recommend our UV Laser Marking Machine and Hybrid Laser Marking Machine for your laser cleaning because of their high absorption levels and efficiency.
If you want to learn more about how laser cleaning can be integrated into your toolbox, check out our laser cleaning page to learn more. More of a hands-on learner? Contact us today for more information.
We’re here to provide you with more details.
Reach out today!
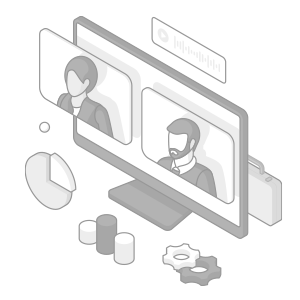